The national lockdowns of 2020 may have helped advance the design and development of the next generation of hyper-efficient city cars, as reorganisation of an annual endurance competition lead one of the teams to re-focus its efforts.
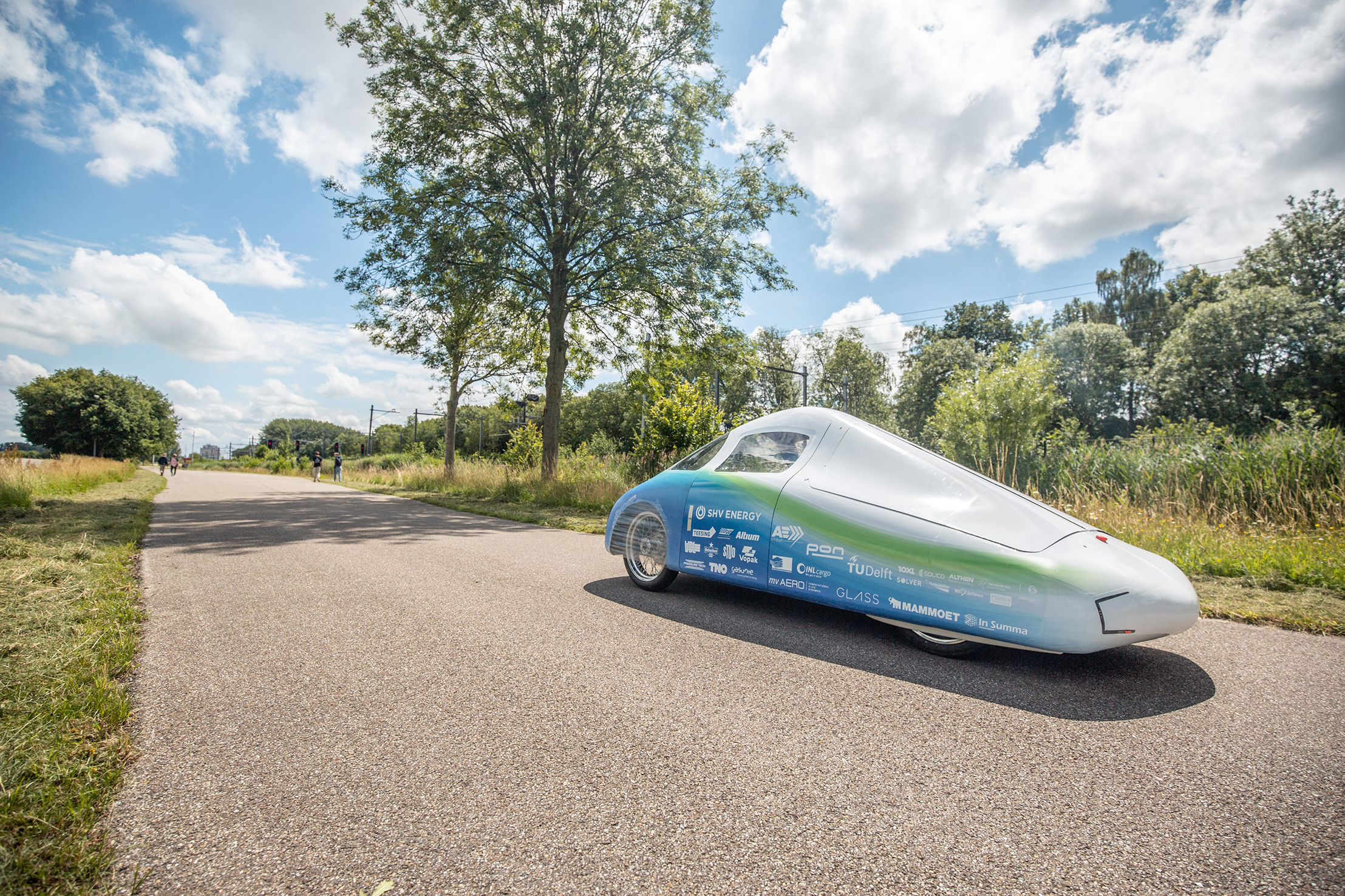
Eco-Runner Team Delft’s new vehicle
Every year since 2005, university-based Eco-Runner Team Delft has developed a new vehicle and entered the Shell Eco-Marathon, competing against many other teams from around Europe to build the world’s most efficient hydrogen-powered car. In this they have always been supported by local engineering company Althen Sensors, who have supplied RWT430 torque sensors, made by British company Sensor Technology Ltd for collecting key data so that the designs can be tested and optimised.
With this year’s competition rearranged due to Covid-19, Team Delft chose to take on an extra challenge: building not just an efficient car but building an efficient city car. This meant that rather than developing a lightweight design optimised to the track-based competition, practical aspects were also taken into consideration and incorporated into the vehicle.
Examples of the new requirements include making a full stop and restart after each lap to simulate driving in urban traffic, and the inclusion of headlights, tail lights, direction indicators and a windscreen wiper. Taking all these new challenges into account, the students started to work towards building the world’s most efficient hydrogen-powered city car.
In order to achieve best results, every single element in the car needs to be as efficient as possible. To this end an aerodynamic body shape based on strong but very lightweight materials was developed. Further efforts were made to ensure an ultra-efficient drivetrain, including customisation of the main drive motor.
In fact ensuring the motor was optimised to the needs of the vehicle’s proving regime was a major part of the overall project. So a special test rig was built so that the motor could be tested at various speeds, through multiple acceleration and deceleration profiles, and over long and short operating periods.
The heart of the test rig was the TorqSense. This is not only a reliable, accurate and easy to used sensor, but because it is non-contact set-up times before each test run are minimal. Over a long and comprehensive testing regime, these individual time savings add up to a considerable overall reduction in programme duration and also help maintain enthusiasm during what could otherwise be laborious procedures.
TorqSense works using by using radio transmissions to detect the intensity of Surface Acoustic Waves generated by the rotation of the motor’s shaft, which is proportional to the instantaneous torque output of the motor.
By using TorqView software, also developed by Sensor Technology, Team Delft was able to get a good view of the torque capabilities of the motor at different rotational speeds. In addition, they could measure the input voltage and current of the motor controller. Also, the team was able to easily adjust the loads on the test rig to simulate different stages and conditions of the actual track-based vehicle test.
The information on the torque levels and rotational speeds of the motor, gained with the TorqView software, helped to forecast the most efficiency operating conditions of the vehicle. These calculated conditions matched those determined by testing the car on the track, confirming that they had identified the best motor setup. This then allowed the student engineers to determine the different speeds needed for an optimal lap!
In fact Team Delft’s analysis and engineering were so good that they won both the 2020 Shell Eco-marathon Hydrogen Endurance Race with a score of 2506,6 km/kg H2 and the Vehicle Design Award.